Axial-flux motor concept
Prototype of a 3D-printed,carbon-reinforced, light-weight, axial-flux machine.
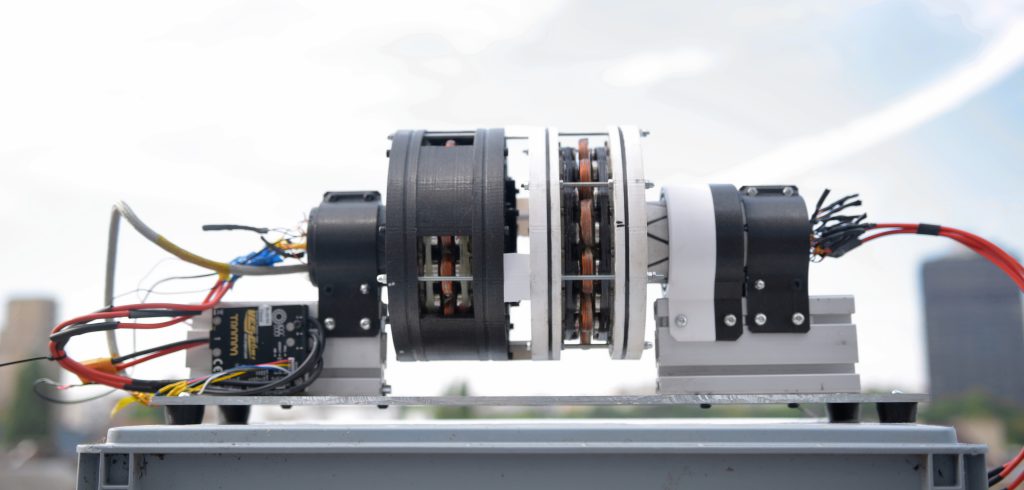
The goal of this project was to:
1-Evaluate the feasability of 3D-printing a brushless motor prototype, as opposed to earlier prototypes built at VUB that are built from aluminium CNC-machined parts. A 3D-printed motor would allow for faster prototyping and allow for more complex geometry such as internal cooling channels.
2-Create a power/efficiency benchmark for a light-weight, coreless axial-flux motor. A coreless air-cooled axial-flux motor would need to be larger than a similar motor with steel cores for the same power output. However, the coreless version could potentially be lighter per kilowatt than the steel-core version, if you can build a light-weight, large-diameter frame.
3-Get experience in the practical prototyping aspects of axial-flux motors.
Interest/possible applications are:
-Use as a motor for an electric one-off vehicle.
-Use as a light-weight, no-gear generator for a small wind turbine.
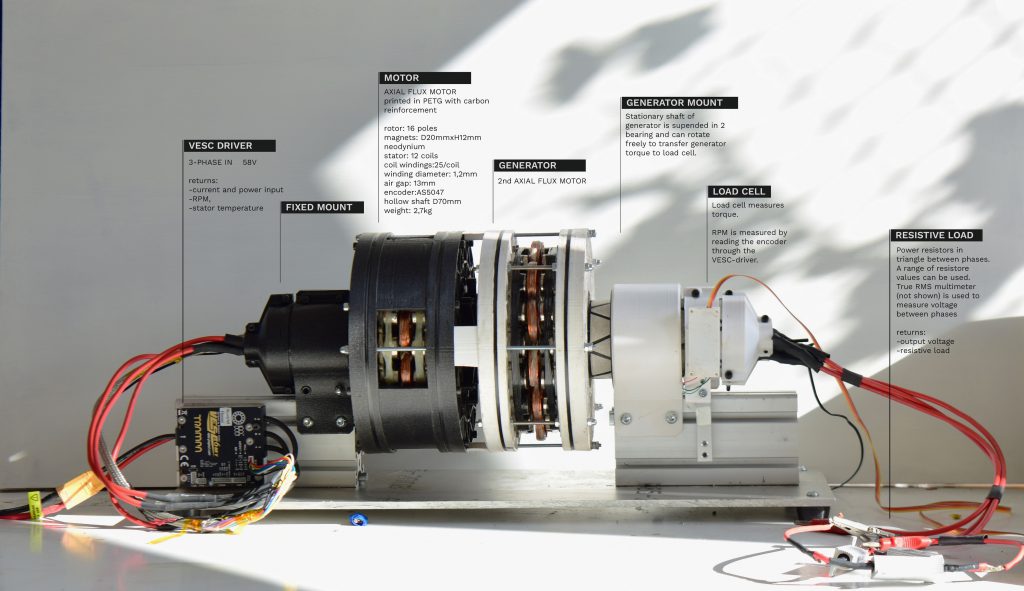
Test setup, black machine is driven with a VESC-driver, white machine has a triangular 3-phase resistive load. Both machines have encoders, and a temperature sensor embedded in the stator. The white machine is mounted on rotating mount so the resulting torque cqn be measured with a load cell. Output current and voltage is measured with multimeters.
Specifications
16 magnet poles on 2 rotor disks
Number of poles:16
Magnets: 20mmDx12mmH round magnets
Shaft diameter: 70mm diameter, hollow
Bearings: SKF 61814 – ID70mm OD80mm
Number of coils:12 – 25 windings per coil – copper diameter:1.2mm
Stator thickness: 8mm designed/10mm as built – air gap 13mm
Mass: 2,7kg of which 68% active materials
Diameter: 200mm
Magnet ring diameter: 150mm
Steel backplate: 3mm
Driver: VESC
Encoder: AS5047
All parts fit on a Prusa I3 mk3 print bed. Printed in PETG
HOLLOW SHAFT
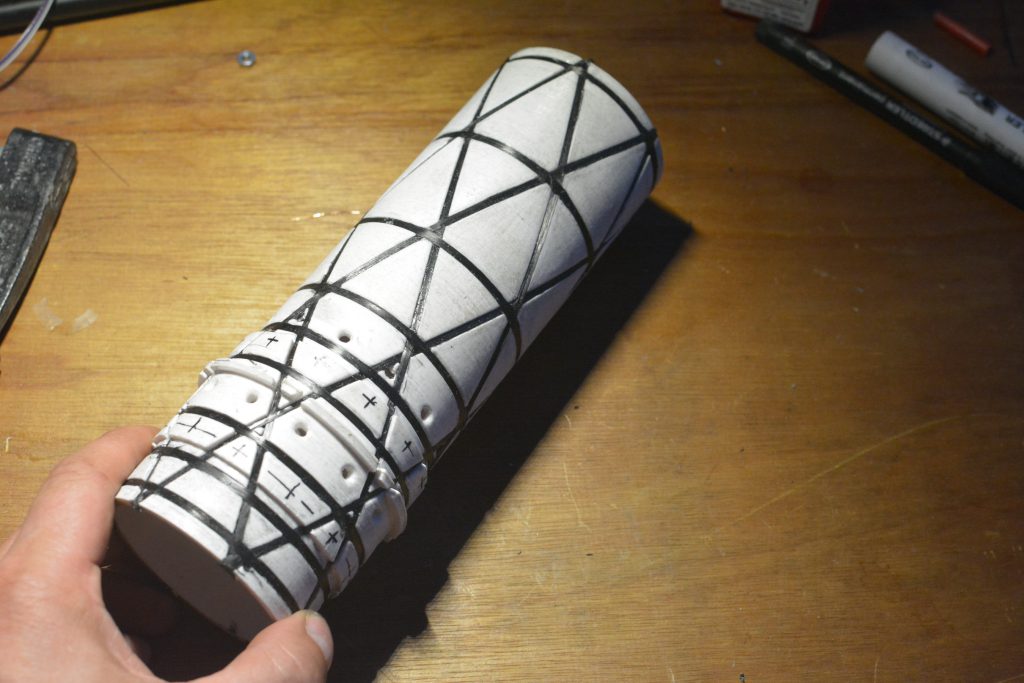
STATOR DISK
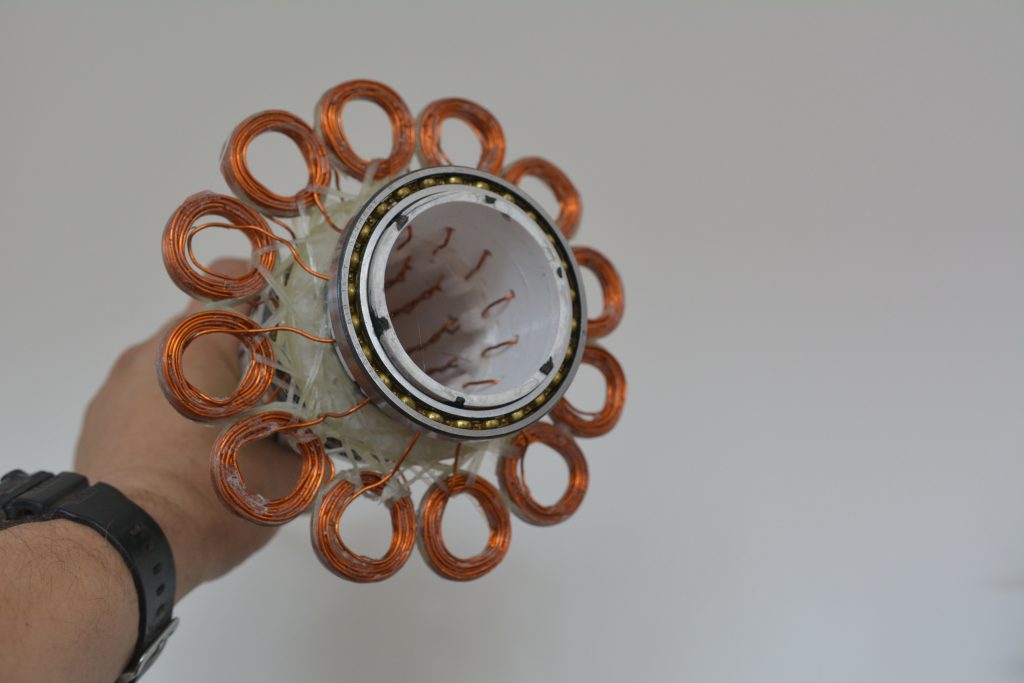
ROTOR DISK
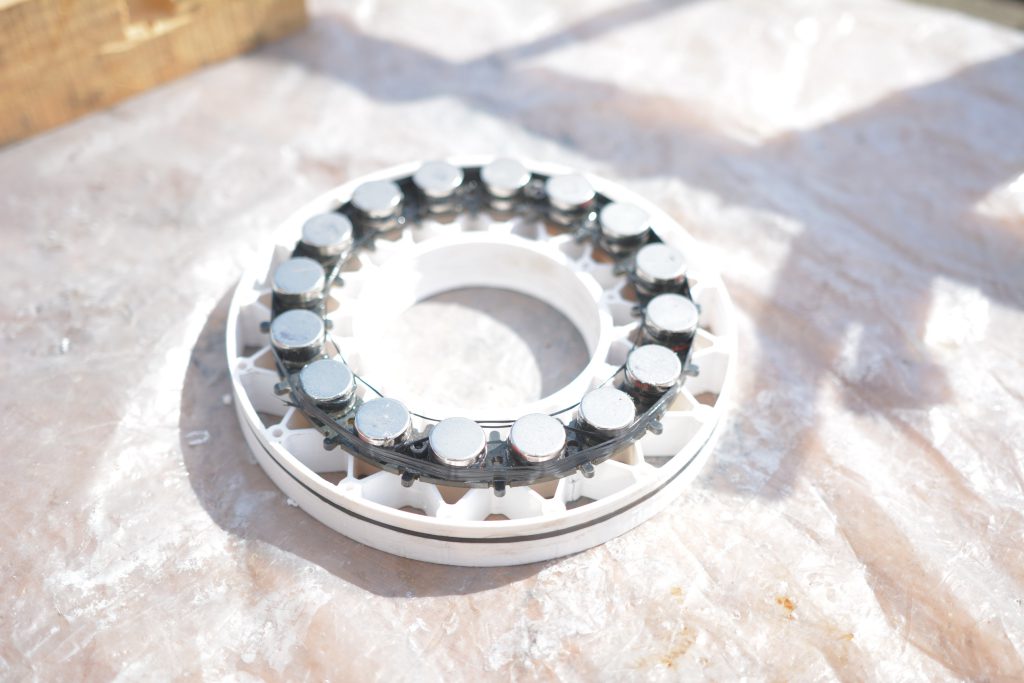
